- تاریخ انتشار ۲۶ مرداد ۱۳۹۹
- تعداد بازدید 19127 بازدید
- دسته بندی مقالات روشهای تولید
/ مقالات ماشین آلات صنعت پلاستیک - نظرات کاربران 2 دیدگاه
- اشتراک گذاری
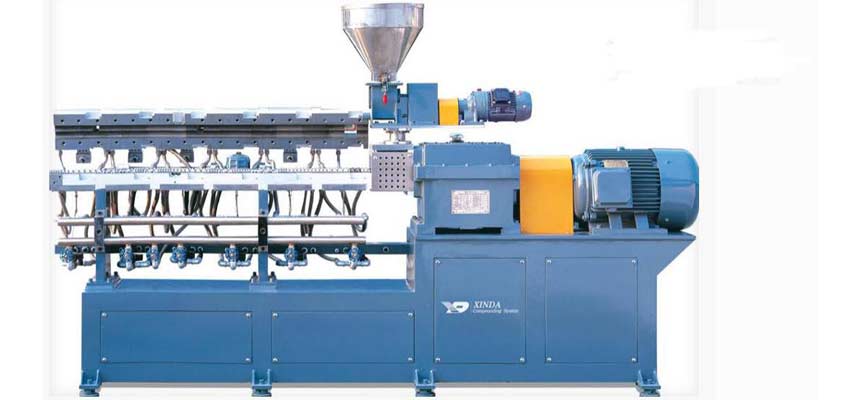
معرفی انواع اکسترودر (Extruder) و روش کار آن+ویدیو
اکسترودر چیست؟ معرفی انواع دستگاه اکسترودر و اجزای آن
با افزایش نیاز به تولید محصولات پلاستیکی، تجهیزات و تکنولوژی تولید این محصولات نیز روز به روز پیشرفت کردهاند. اکسترودر، به عنوان یکی از مهمترین دستگاههای تولید محصولات پلاستیکی، همواره مورد توجه تولیدکنندگان، چه در حوزه تولید گرانول و چه در حوزه تولید محصولات پلاستیکی تمامشده بوده است. برای تولید محصولات پلاستیکی، گرانول را وارد دستگاه اکسترودر (اکستروژن) کرده و پس از ذوب آن، تبدیل به محصولات دلخواه میشود. در این مقاله به بررسی این موضوع که «اکسترودر چیست»، «چه اجزایی دارد» و «چگونه کار میکند» خواهیم پرداخت. با ما همراه باشید.
اکسترودر (Extruder) چیست؟
اکسترودر دستگاهی است که برای اکسترود (روش اکستروژن) انواع مواد پلاستیکی و تولید محصول تمامشده مورد استفاده قرار میگیرد. اکستروژن یکی از روشهای شکلدهی است که برای کاهش ضخامت یا سطح مقطح مواد به کار میرود. اگر بخواهیم سادهتر توضیح دهیم، دستگاه اکسترودر را همانند یک سرنگ در نظر بگیرید که در بخش بزرگتر (مخزن اصلی سرنگ) مذاب پلیمر وارد میشود و تحت فشار، از سر نازکتر سرنگ (اکسترودر) خارج میشود و محصول نهایی شکل میگیرد. اکستروژن روش بسیار انعطاف پذیری است و با استفاده از مواد اولیه ورودی مناسب میتوان طیف وسیعی از تولیدات را تهیه کرد. اکسترودر میتواند به عنوان دستگاه گرانول ساز در تولید انواع گرانول و یا به عنوان دستگاهی برای تولید محصول تمامشده مورد استفاده قرار بگیرد.
انواع اکسترودر
با توجه به اجزای به کار رفته در تولید اکسترودر، این محصول میتواند انواع مختلفی داشته باشد. در ادامه به بررسی انواع اکسترودر میپردازیم.
اکسترودر تک ماردونه (One Screw Extruder)
اکسترودر تک ماردون (تک پیچه) یکی از متداولترین اکسترودرهای موجود در بازار برای شکلدهی پلاستیکهاست که از یک ماردون در داخل یک سیلندر تشکیل شده است. پلاستیکها معمولاً به صورت دانهای شکل (گرانول) یا خاکه نرم از قیف به سمت ماردون و سیلندر تغذیه میشوند و عملیات شکلدهی انجام میشود.
اکسترودر دو ماردونه (Two Screw Extruder)
در سالهای اخیر استفاده از اکسترودرهای دوماردونه (دوپیچه) که در داخل محفظه داغ اکسترودر حرکت چرخشی دارد، افزایش یافته است. این دستگاهها در مقایسه با اکسترودرهای تکماردونه تفاوتهایی در نرخ خروجی، بازده اختلاط، حرارت تولیدشده و نظایر آن نشان میدهد. خروجی اکسترودر دوماردونه معمولاً سه برابر اکسترودر تک ماردونه ای با همان قطر و سرعت است. اگرچه اصطلاح ماردون دوقلو اصطلاحی بین المللی برای اکسترودرهای دو ماردونه است؛ اما دو ماردون لزوماً یکسان نیستند.
در واقع انواع گوناگونی از این دستگاه موجود است. ماردونها ممکن است به صورت جفتشده (Conjugated) یا جفتنشده (Non-Conjugated) باشند. در حالت جفتنشده، بین پلکانهای ماردون فضای خالی وجود دارد که امکان حضور مواد را نیز فراهم میکند. در اکسترودر دو ماردونه با جهت چرخش مخالف یکدیگر، مواد دچار برش و فشردگی میشوند (نظیر آنچه در غلتکرانی رخ میدهد؛ یعنی مواد بین غلتک هایی با جهت چرخش متفاوت، فشرده می شود).
در اکسترودر حاوی دو ماردون با جهت چرخش یکسان، مواد از یک ماردون به دیگری منتقل می شود. این گونه آرایش برای مواد حساس به حرارت کاملاً مناسب است؛ زیرا مواد در اکسترودر به سرعت منتقل می شود بدون اینکه کمترین احتمال ماندگار شدن موضعی (Entrapment) مواد وجود داشته باشد. حرکت مواد در اطراف ماردونهای جفتنشده کمتر (کندتر) است ولی نیروی جلوبرنده (Propulsive) بزرگتر است.
اجزای اکسترودر
زمانی که از اکسترودر صحبت میکنیم، منظورمان مجموعه محفظه (سیلندر) و ماردون است که میتوان آن را به عنوان بدنه و واحد اصلی تولید قطعاتی با اشکال مختلف به کار برد. مذاب پلیمر درون سیلندر قرار میگیرد و با استفاده از ماردون به سمت جلو هدایت میشود تا به دریچه خروجی (دهانه قالب) برسد. اکسترودرها به دو دسته اکسترودر تک ماردونه و اکسترودر دو ماردونه تقسیم میشوند. اکسترودر دو ماردونه سه قسمت مجزا دارد: ناحیه تغذیه (Feed Zone)، ناحیه تراکم و فشردگی (Compression Zone) و ناحیه اندازهگیری و سنجش.
تصویر زیر، نمایی از قطعات و اجزای اکسترودر را نشان میدهد.
اکسترودر از اجزای اصلی زیر تشکیل میشود:
- ناحیه تغذیه (Feed Zone): کار این ناحیه، دادن گرمای اولیه به پلاستیک و انتقال آن به نواحی بعدی است. طراحی این ناحیه حائز اهمیت است. زیرا عمق ثابت ماردون طوری انتخاب شود که مواد لازم و کافی را به ناحیه اندازه گیری (Metering Zone) تغذیه کند؛ به طوری که نه دچار گرسنگی شود و نه در اثر زیاد بود ن مواد، لبریز و پس زده شود. طراحی مناسب (Optimum) و متعادل، به طبیعت و شکل مواد تغذیه شونده (Feedstock)،شکل هندسی (Geometry) ماردون و خواص اصطکاکی پلاستیک نسبت به ماردون و محفظه بستکی دارد. رفتار اصطکاکی مواد تغذیه شده، تاثیر قابل توجهی بر آهنگ ذوب شدن مواددارد.
- ناحیه تراکم و فشردگی (Compression Zone): در این ناحیه، عمق ماردونه به تدریج کاهش می یابد که موجب متراکم شدن و فشردگی پلاستیک می شود. این فشردگی دو نقش عمده ایفا می کند؛ یکی آنکه هوای محبوش در داخل مواد را به ناحیه تغذیه می راند و دیگر آنکه انتقال حرارت را با کاهش دادن ضخامت مواد بهبود می بخشد.
- ناحیه اندازه گیری و سنجش: در این ناحیه، عمق ماردونه یکسان و ثابت، اما بسیار کمتر از عمق ناحیه تغذیه است. در این ناحیه، مذاب به صورت همگون و یکنواخت در می آید به طوری که با آهنگ ثابتی، در درجه حرارت و فشار یکسان و ثابت، به حدیده تغذیه می شود. این ناحیه به سهولت و سادگی تحلیل و ارزیابی می شود؛ زیرا مشتمل بر جریان مذاب گرانروان در داخل مجرایی با عمق و ابعاد ثابت است. طول نواحی سه گانه ماردون خاص، بستگی به ماده ای دارد که تحت اکستروژن قرار می گیرد. برای نمونه نایلون خیلی سریع ذوب می شود، به طوری که تراکم و فشردگی مذاب در طول یک گام از ماردون نیز قابل تامین است.
- سایر اجزای فرعی اکسترودر: در اکسترودرهای تجاری، اجزا و نواحی اضافی برای بهبود کیفیت محصول به ماردون افزوده میشود. به عنوان نمونه، ناحیه اختلاطی (Mixing Zone) مشتمل بر پلکان هایی (Flights) با گام کمتر یا معکوس، به منظور کسب اطمینان از یکنواختی مذاب و کافی بودن آن در منطقه اندازه گیری، استفاده می شود. برخی از اکسترودرها ناحیه هواگیری (منفذ خروج هوا) وجود دارد. وجود این ناحیه به این دلیل است که برخی پلاستیک ها جاذب رطوبت (Hygroscopic) هستند
دلیل وجود ناحیه هواگیری در اکسترودر و مشکلات عدم وجود آن
در برخی از اکسترودرها ناحیه هواگیری (منفذ خروج هوا) وجود دارد. وجود این ناحیه به این دلیل است که برخی پلاستیکها جاذب رطوبت (Hygroscopic) هستند؛ یعنی از محیط اطراف خود رطوبت جذب میکنند و اگر به همین صورت مرطوب در اکسترودر فاقد ناحیه هواگیری استفاده شوند، کیفیت محصول نهایی خوب نیست؛ زیرا در داخل مذاب، بخار آب محبوس می شود. 2 راه حل برای رفع این مشکل وجود دارد:
- راه حل اول: برای رفع این مشکل راهحل آن است که مواد تغذیهشونده به اکسترودر را قبلاً خشک کنیم. این روش گران و پر هزینه است و امکان آلودگی نیز در مواد ایجاد می کند.
- راه حل دوم: روش دوم، استفاده از محفظه های منفذدار (Vented Barrels) است. در اولین قسمت ماردون، مواد که به صورت دانه بندی است، پس از ورود مواد ذوبشده، سپس به طریق معمول فشرده و همگن میشود. آنگاه با ورود به ناحیه غیر فشردگی (Decompression-Zone)، فشار مذاب به محیط کاهش مییابد؛ این عمل، امکان خروج و گریز بخار و سایر مواد فرّار را از داخل مذاب به خارج اکسترودر، از طریق منفذ تعبیه شده در بدنه اکسترودر فراهم میکند. در نتیجه مذاب در طول محفظه به ناحیه دوم فشردگی هدایت میشود تا از محبوس شدن هوا در مذاب ممانعت به عمل آید.
صافی (Gauze Filter) و نقش آن در کیفیت تولید محصول نهایی
یکی دیگر از اجزای مهم اکسترودر، صافی (Gauze Filter) پس از ماردون و پیش از ورود مذاب به دهانه قالب است. این صافی به صورت کاملاً موثری هرگونه مواد ناهمگون و ناخالصیها را از مذاب جدا میکند. عدم وجود آن حتی ممکن است موجب انسداد قالب شود. این صفحات صاف و غربالکننده معمولاً مذاب را تا مقیاس 120 تا 150m صاف و تصفیه میکنند.
اما شواهد موجود نشان میدهد که ذراتی کوچکتر از مقیاس فوق، موجب شروع ایجاد ترکهای مویین در تولیدات پلاستیکی نظیر لولههای تحت فشار پلی اتیلنی میشود. برای چنین مواردی صافی های بسیار ظریفی در مقیاس 45m به کار میرود که به گونهای موثر و جالب توجه، کیفیت و عمر مفید محصول را بهبود میبخشد.
از آنجا که این صافیهای ظریف آسیبپذیر است، توسط صفحه سرعتشکنی (Breaker plate) هدایت میشود. این صفحه تعداد زیادی سوراخهای مماس بر یکدیگر و بسیار تنگاتنگ دارد که بدون اینکه به ذرات جامد سوخته (Dead-Spots) احتمالی همراه با مذاب اجازه ورود دهد، مذاب را عبور میدهد.
این صفحه سرعت شکن همچنین جریان مذابی را که پس از خروج به صورت حلزونی در آمده است خطی می کند. چون منافذ این صافی های ظریف به تدریج بسته می شود، پی در پی باز شده، تعویض می شود. در بسیاری از اکسترودرهای پیشرفته با صافیهای ظریف، کار تعویض آنها بدون نیاز به توقف اکسترودر صورت می گیرد.
همچنین باید خاطر نشان کنیم که اگرچه این وظیفه اصلی صفحه سرعت شکن و صاف نیست؛ اما این قطعه به ایجاد فشار معکوسی که موجب بهبود اختلاط مذاب می شود کمک میکند. چون فشار در قالب حائز اهمیت است، شیری (valve) پس از صفحه سرعت شکن در اکسترودر وجود دارد که امکان تنظیم لازم را فراهم میآورد.
اکسترودر چگونه کار میکند؟
به طور کلی، شیوه کار اکستروژن به این شکل است که ابتدا، گرانول از طریق قیف به سمت ماردون و سیلندر تغذیه میشود. سپس به وسیله ماردون در طول محفظه حرکت میکند و در اثر حرارت ناشی از گرمکنندههای محفظه (Barrel Heaters) و اصطکاک ناشی از حرکت بر روی لبههای ماردون و دیواره سیلندر گرم میشود و به مذاب تبدیل میشود.
عمق معبر (Channel-Depth) در طول ماردون کاهش یافته و موجب فشرده شدن مواد میشود. در انتهای محفظه اکسترودر، مذاب با عبور از قالب که در دهانه اکسترودر قرار دارد به شکل مورد نظر برای محصول نهایی در میآید. همانطورکه بعدا خواهیم دید، به دلیل امکان استفاده از قالبهای مختلف، امکان تولید قطعات با اشکال مختلف بوسیله اکسترودر وجود دارد.
چگونگی جریان (Mechanism of flow) در اکسترودر
جریان مذاب در اکسترودر پروسه پیچیدهای دارد و ممکن است حالتهای مختلفی داشته باشد. مرحله اول، ذوب پلاستیک در اکسترودر است. پلاستیک با حرکت در طول ماردون به صورت زیر ذوب میشود:
نخست لایه نازکی (Thin Film) از ماده مذاب در جداره محفظه تشکیل می شود. با چرخش ماردون این لایه از جداره محفظه کنده شده به قسمت جلوی پیکان ماردون انتقال مییابد و وقتی که به سطح خود ماردون (Core of screw) میرسد، دوباره به طرف بالا جاروب میشود. بدین ترتیب حرکت چرخشی در جلوی پیکان ماردون (پیشانی ماردون) به وجود میآید.
در آغاز، پلکان ماردون حاوی دانههای جامد است که در اثر حرکت چرخشی به داخل حوضچه مذاب جاروب میشود. با استمرار چرخش ماردون، مواد بیشتری به داخل حوضچه مذاب ریخته میشود تا اینکه در نهایت فقط مواد مذاب است که در پلکانهای ماردون اکسترودر وجود دارد.
در اثنای گردش ماردون در داخل محفظه، حرکت مواد در راستای طول ماردون بستگی به چسبندگی مواد به ماردون یا محفظه دارد. به طور نظری در مرز افراط و تفریط (Extremes) وجود دارد. در حالت اول فقط مواد به درون ماردون چسبیده است، در نتیجه ماردون و مواد مانند استوانه توپر و جامدی در داخل محفظه می چرخد. در این حالت نامناسب هیچ خروجی وجود ندارد. در حالت دوم، مدار روی ماردون می لغزد و مقاومت زیادی در برابر گردش ماردون در داخل محفظه به وجود می آورد. در این حالت حرکتی در جهت محور دستگاه برای مذاب فراهم میشود که بهترین حالت ممکن است. در عمل، رفتار واقعی، حالتی بین دو واحد است زیرا مواد هم به ماردون و هم به بدنه اکسترودر میچسبد.
خروجی مناسب ناشی از به وجود آمدن جریان کشنده و جلو برندهای (Drag flow) در اثر چرخش ماردون و سکون محفظه است که به حرکت سیال گرانروان بین دو صفحه موازی شباهت دارد که در آن صفحه ای ثابت و صفحه دیگر دارای حرکت است. علاوه بر این، جریان دیگری هم ناشی از اختلاف فشار بین دو انتهای ماردون است وجود دارد وبه این دلیل که حداکثر فشار در انتهای اکسترودر به وجود می آید، جریان فشاری (Pressure flow) خروجی را کاهش می دهد. همچنین به دلیل فاصله (Clearance) که بین پلکانهای ماردون و بدنه اکسترودر وجود دارد اجازه نشتی به مواد در جهت عکس امتداد ماردون داده، به طور موثری خروجی گاز را کاهش می دهد.
فرار و گریز مواد به سمت عقب ماردون در حالتی که ماردون فرسوده (Worn) باشد بیشتر است. گرما یا سرمای خارج اکسترودر نیز نقش مهمی در نحوه ذوب شدن مواد ایفا می کند. در اکسترودرهایی که دارای خروجی زیادی هستند، مواد، طول محفظه اکسترودر را سریع می کند. در نتیجه گرمای ذوب شدن کامل در اثر عمل برش تولید می شود و به استفاده از حرارت دهنده های خارجی محفظه اکسترودر نیازی نیست. بنابراین در این حالت اگر گرمای زیادی در مذاب به وجود آمده باشد سرد نگه داشتن محفظه حائز اهمیت است. در برخی مواقع خنک کردن ماردون اکسترودر نیز لازم است که البته اثری بر درجه حرارت مذاب ندارد.
اما اثر مالشی (اصطکاکی) بین پلاستیک و ماردون را کاهش می دهد. در همه اکسترودرها خنک کردن محفظه اکسترودر در ناحیه تغذیه ضروری است و لازم است تا بتوان اطمینان کاملی از تغذیه بدون درد سر مواد به اکسترودر به دست آورد. طبیعت و حالت گرمایی مذاب در اکسترودر با دو حالت ترمودینامیکی مقایسه می شود.
اولی حالت بی دررو (Adiabatic) است؛ به این مفهوم که سیستم کاملاً مجزا از محیط خارج است و هیچ جذب و دفع حرارتی در آن رخ نمی دهد. اگر این حالت مطلوب در اکسترودر حاکم نباشد، فقط مقداری کار لازم است روی مذاب انجام شود تا گرمای معین تولید کند که به ازاء آن هیچ ضرورتی به گرم یا سرد کردن دستگاه نباشد.
حالت مطلوب دوم، به همدما (Isothermal) موسوم است که در این حالت، درجه حرارت در تمام نقاط مذاب یکسان است و در نتیجه محفظه به گرم کردن و سرد کردن مستمر و دائمی برای جبران هرگونه اتلاف یا اخذ حرارت از مذاب برای ثابت ماندن دما نیاز دارد.
در عمل، عملیات حرارتی در اکسترودرها بین دو حالت مرزی فوق قرار دارد. اکسترودرها ممکن است بدون هیچ حرارت دهنده یا سرد کننده خارجی کار کنند. لیکن در واقع در این صورت بی در رو نیست؛ زیرا اتلاف حرارت به وقوع می پیوندد. از طرف دیگر با حالت همدما در تمام طول اکسترودر مواجه نیستیم زیرا دانه های جامد نسبتاً سردی به اکسترودر تغذیه می شود. اما برخی از نواحی اکسترودر ممکن است خیلی نزدیک به حالت همدما باشد.
ویدیو نحوه کار دستگاه اکسترودر
همانطور که قبلتر توضیح داده شد، نحوه کار اکسترودر همانند یک سرنگ است. طی فرآیند حرارت دادن، گرانول به مذاب تبدیل میشود و در سیلندر اکسترودر، به وسیله ماردون به سمت دهانه قالب هدایت میشود و پس از خروج از اکسترودر و سرد شدن، محصول نهایی تولید میشود. ویدیوی زیر، مراحل تولید به وسیله اکسترودر را نشان میدهد.
روشهای شکلدهی با استفاده از اکسترودر
اکستروژن روشی بسیار انعطاف پذیری است و با استفاده از حدیده مناسب می توان طیف وسیعی از تولیدات را تهیه کرد. برخی از این روش های بسیار متداول را در اینجا ذکر می کنیم:
- تولید گرانول
- تولید پروفیل
- تولید فیلم های دمشی بسیار نازک (Film blowing)
- قالب گیری دمشی (Blow Molting)
نکات مهم درباره تولید به روش اکستروژن
اکسترودر، میتواند یکی از بخش های مهم دستگاه تزریق پلاستیک باشد و از نظر فرایند کاری، شبیه به این دستگاه است. یکی از مهمترین ویژگی پلیمرها و به ویژه پلاستیک ها سهولت شکل پذیری آنهاست. در بعضی حالات، قطعات نیمه کاملی نظیر ورقه ها یا میله های تولید شده، متعاقباً با استفاده از روشهای متداول ساخت، مانند جوشکاری یا ماشین کاری به قطعه نهایی تبدیل می شود. اما در بسیاری مواقع، قطعه نهایی، علیرغم برخورداری از شکلی کاملاً پیچیده، طی یک مرحله تولید می شود.
عملیات حرارت دادن، شکل دادن و خنک کردن ممکن است (مانند تولید لوله به روش اکستروژن) به دنبال یکدیگر و بدون وقفه (Continuous) انجام شود و یا ممکن است طی مراحلی ناپیوسته، زمانگیر و تکرار شونده (مثل عملیات تولید تلفن خانگی به روش قالبگیری تزریقی یا دستگاه تزریق) صورت پذیرد که در اکثر موارد، فرایند به طور خودکار انجام شده برای تولید انبوه بسیار مناسب است.
طیف وسیعی از روشهای شکل دهی برای پلاستیک ها و پلیمرهای شکل پذیر کاربرد دارد. در بسیاری از حالات انتخاب روش به چگونگی شکل نهایی قطعه و گرما نرم یا گرما سخت بودن ماردون بستگی دارد.
بنابراین در عملیات طراحی، آگاهی طراح از روش های متنوع شکل دهی، حائز اهمیت است زیرا اشکال ناجور و نامناسب قطعه و یا مسائل جزئی کار طراحی، ممکن است محدودیت هایی در انتخاب روش قالبگیری برای طراح ایجاد کند. دسته بندی اکسترودرهای متداول این دسته بندی شامل گونه های زیر می شود.
ویکی پلاست | مرجع بازار صنعت پلاستیک
نظرات کاربران
سمیرا روشن ارسال پاسخ
-
ارزش ذهن۳۰ ثانیهای به سبک «چارلی مانگر»
ادامه مطلب -
مهارتهای نرم، سرمایه پنهان سازمانها در جذب و نگهداشت نیروی انسانی
ادامه مطلب -
پلیمرهای عمومی و مهندسی پرکاربرد در بازار ایران
ادامه مطلب -
چگونه «نه» بگویید تا اعتبارتان خدشهدار نشود
ادامه مطلب -
چه زمانی باید پلهای پشت سرتان را خراب کنید؟
ادامه مطلب -
کدام مشاغل در معرض خطر ناپدید شدن طی ۲۰ سال آینده هستند؟
ادامه مطلب
-
آشنایی با فواید و مزایای پلاستیک در زمینههای متفاوت
ادامه مطلب -
مشکلات تزریق پلاستیک چیست و عیبیابی قطعه چگونه انجام میشود؟
ادامه مطلب -
نشانههای رفتارهای تلافیجویانه از سوی کارفرما
ادامه مطلب -
کار کمتر نتیجه بیشتر
ادامه مطلب -
در برابر نسل زد، شیوههای سنتی مدیریت را کنار بگذارید
ادامه مطلب -
چگونه «نه» بگویید تا اعتبارتان خدشهدار نشود
ادامه مطلب
-
پی وی سی (PVC) چیست؟ آشنایی با کاربرد و ویژگیهای پلی وینیل کلراید
ادامه مطلب -
پلاستیک مهندسی چیست
ادامه مطلب -
نایلون چیست؟ تفاوت نایلون و نایلکس
ادامه مطلب -
بازیافت پلاستیک: آشنایی با انواع بازیافت پلاستیک و مراحل آن
ادامه مطلب -
گرانول چیست؟ مقاله جامع آشنایی با انواع گرانول و ویژگیهای آن
ادامه مطلب -
دستگاه تزریق پلاستیک چیست؟ آشنایی با انواع دستگاه ها، اجزا و کاربردها
ادامه مطلب